Be meaning to do this for a while so finally got round to testing my J-Line IC pressure drop across the core.
I am using a Dywer's Magnehelic differential gauge. This gauge has two pressure inputs on the back. One port for measuring above atmospheric pressure and the other port for measuring below atmospheric pressure, vacuum in other words.
With one port connected it measures the input pressure verse the open port-atmospheric.
Connect both ports across the core, hot charge pipe and cold charge pipe, it will measure the pressure difference.
I then took the vehicle out on the road and did a few red line pulls. Hint, play the YouTube clip in the highest HD and in Theatre mode and you can just get a idea of whats happening with the gauge readings.
I also did a 3rd gear and 4th gear roll-on showing the response of the EFR 6258 turbo.
The maximum pressure drop was very close to 2psi.
3rd gear response, 20psi by 3500 rpm.
4th gear response, 20psi by 3165 rpm
[video]https://youtu.be/vry4_-4Eg50[/video]
I would appreciate if someone can load the clip because for some reason I can not do this anymore on my PC.
[video=youtube;vry4_-4Eg50]https://www.youtube.com/watch?v=vry4_-4Eg50[/video]
I am using a Dywer's Magnehelic differential gauge. This gauge has two pressure inputs on the back. One port for measuring above atmospheric pressure and the other port for measuring below atmospheric pressure, vacuum in other words.
With one port connected it measures the input pressure verse the open port-atmospheric.
Connect both ports across the core, hot charge pipe and cold charge pipe, it will measure the pressure difference.
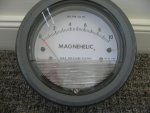
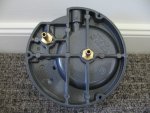
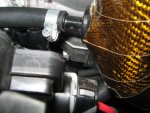
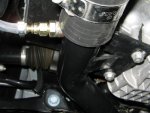
I then took the vehicle out on the road and did a few red line pulls. Hint, play the YouTube clip in the highest HD and in Theatre mode and you can just get a idea of whats happening with the gauge readings.
I also did a 3rd gear and 4th gear roll-on showing the response of the EFR 6258 turbo.
The maximum pressure drop was very close to 2psi.
3rd gear response, 20psi by 3500 rpm.
4th gear response, 20psi by 3165 rpm
[video]https://youtu.be/vry4_-4Eg50[/video]
I would appreciate if someone can load the clip because for some reason I can not do this anymore on my PC.
[video=youtube;vry4_-4Eg50]https://www.youtube.com/watch?v=vry4_-4Eg50[/video]